Objective
Protect sub-structure portion of bulk cargo terminal pier from corrosion.
Highlights
Successfully encapsulated 500 piles over three seasons
Completed project with no vessel shutdown of the pier during construction
Designed and installed 20-year impressed-current cathodic protection system
Developed and utilized three separate high-pressure cleaning systems
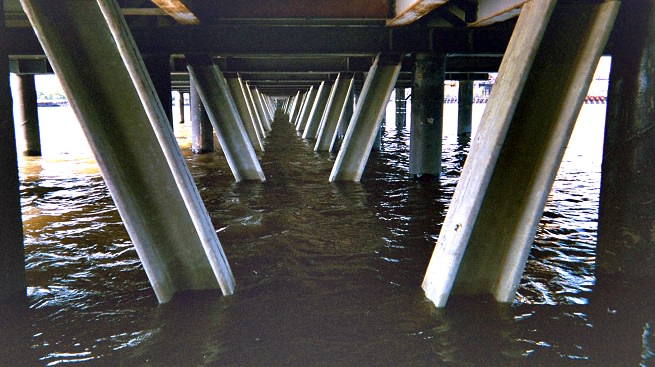
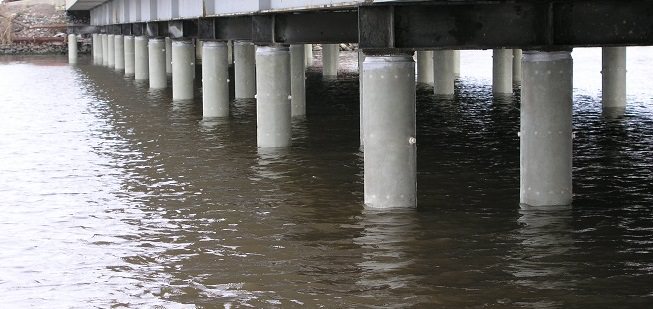
Project Details
Substructure was contracted to protect a bulk cargo terminal from corrosion. Corrosion can be countered through sacrificial-anode systems, impressed-current systems, marine coatings, and encapsulations. After careful evaluation of the size and location of the facility and considering the environmental conditions, Substructure developed a program for the client to encapsulate its 500 support and batter piles and install an impressed-current cathodic protection system. This provided the facility total corrosion protection, from below the pile cap to the seafloor.
For the pile encapsulation, which targets corrosion in the intertidal zone, Substructure encapsulated three different size/shape piles, employing our patented epoxy pump. All piles were steel, two round piles and one H-shaped pile. Substructure designed specialized semi-automated surface preparation systems utilizing 20,oooPSI water. The cleaning systems were designed for each size and style of pile to consistently prepare the surface that would enable the strongest adhesion with the epoxy. The cleaning produced a near bight-white surface, exceeding the minimum standards for a WJ1 surface preparation. Substructure’s experienced installation crew were able to quickly and efficiently install jackets, apply custom-built form clamps, and inject each pile in a single lift. Epoxy injection took place in the same shift as the surface preparation - typically within a 6 hour window. Epoxy encapsulation performed under these rigorous and high standards can protect the structure of the pile by over 20 years.
To target corrosion below the encapsulations, Substructure designed and installed the impressed-current cathodic protection (CP) system. Substructure designed the impressed-current systems to produce highly efficient current distribution patterns throughout the facility. The well-designed system took into consideration environmental factors, existing pier conditions, and predicted future coating failures to determine conservative life cycle consumption of the system. The system is designed soundly protect the facility for up to 20 years. Substructure installed 250 anodes for this facility over a one and a half month time period during encapsulation construction. Substructure maintains the cathodic protection system which continues to run flawlessly.